Efficient and cost competitive heat exchangers
Two separate heat exchanger trains are needed to implement the innovative power plant concept:
- Low-temperature heat exchanger (L-HEX), needed for the adiabatic CAES, and
- High-temperature heat exchanger (H-HEX), needed to heat and reheat the air before expansion across the turbines.
The appropriate heat exchanger design is more an implementation than a technological challenge, as the necessary equipment can be obtained by combining available high-TRL solutions.
For both HEX trains, two different design approaches will be addressed and evaluated to find the most suitable solution:
- The first option is based on conventional indirect recuperative heat exchangers (e.g. shell-and-tube layout)
- The second approach will study a direct contact regenerative heat exchanger concept, in order to reduce size and costs (e.g. cordierite ceramic honeycomb structures)
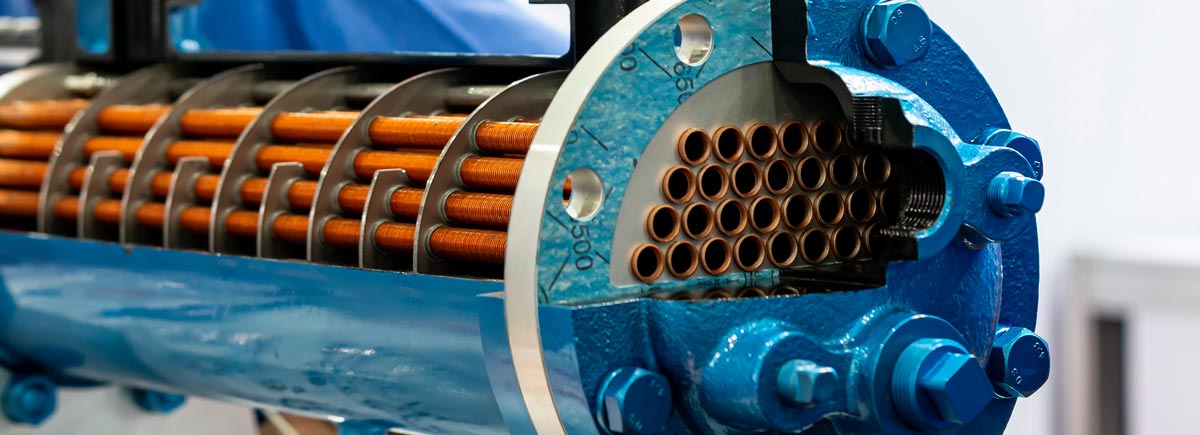
Compressor/expander design for small-scale and large-scale applications
Turbomachinery is a key-enabling technology for CAES systems. The typical operating conditions of CAES pose numerous challenges to the efficient design and performance of compressors and turbines, setting the need to find an optimal solution balancing trade-offs between efficiency, reliability, costs, and economics.
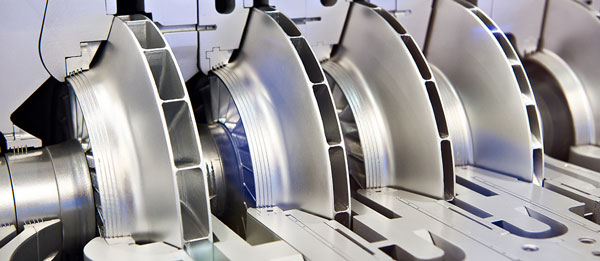
Air storage pressure is significant – up to 150 bars. The project will analyse three technological approaches in order to find the best air compressor solution:
- Multi-stage, intercooling reciprocating compressors
- Multi-stage, intercooled (barrel) centrifugal compressor
- Multi-stage, adiabatic axial compressor followed by single or multi-stage centrifugal compressors
The final selection process will involve trade-offs that will be carefully studied when optimising the system. For regions where two technologies are possible, a techno-economic-environmental optimisation will be carried out to determine the compressor type enabling the highest global system performance. The key challenge is a variable overall pressure ratio as the storage pressure builds up during charging.
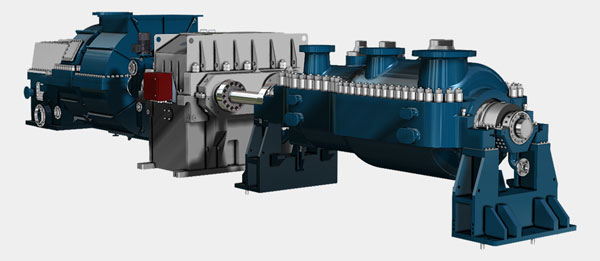
The same problem with variable pressure ratio applies to expanders (turbines), too. However, in this case, there is an additional degree of complexity brought about by the high inlet pressure.
An easy solution to compensate for the variable pressure ratio, ensuring safe operation and maximising performance is not available. This will be studied in the project through the incorporation of control elements and series/parallel arrangement of multistage expanders to yield an adaptive operating strategy accommodating a decreasing expansion ratio.
ASTERIx-CAESar project will explore parallel routes for the turbines:
- Adapting existing equipment, as well as
- Developing turbines specific to the CAES concept proposed by the project.